李見明老師簡介
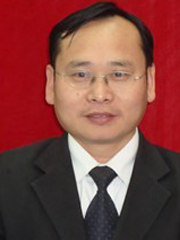
博客訪問:48993
國際認證注冊管理咨詢師(CMC) 經(jīng)濟管理碩士 全面員工關懷模型創(chuàng)始人 精益管理系統(tǒng)導入專家 卓越績效模式導入專家 人力資源管理實戰(zhàn)專家 流程管理實戰(zhàn)導入專家 深圳市市長質量獎評審專家 廣東省政府質量獎評審專家 中國首批公共服務質量獎評審專家 多家平面和網(wǎng)絡媒體特..
李見明最新博文
李見明主講課程
精細化管理內(nèi)涵的再認識和理論淵源
時間:2012-08-10 作者:李見明
一、國內(nèi)專家對精細化管理的認識 從網(wǎng)絡上搜集的資料和出版的圖書來看,對精細化管理的定義,目前是各路諸侯紛呈,人見仁,智見智,沒有統(tǒng)一的認識。目前國內(nèi)對精細化管理認識比較有代表性的幾種觀點: 1、精細化管理是管理者用來調整產(chǎn)品、服務和運營過程的技術方法。 它以專業(yè)化為前提、系統(tǒng)化為保證、數(shù)據(jù)化為標準、信息化為手段,把服務者的焦點聚集到滿足被服務者的需求上,以獲得更高效率、更多效益和更強競爭力。(見汪中求等著《精細化管理》) 2、精細化管理就是要用具體、明確的量化標準取代籠統(tǒng)、模糊的管理要求,把抽象的戰(zhàn)略、決策,轉化為具體的、明確的發(fā)展舉措。 3、精細化管理是以精細操作和管理為基本特征,通過提高員工素質,克服惰性、控制企業(yè)滴漏,強化鏈接,協(xié)作管理,從而提高企業(yè)整體效益的管理方法。 4、精細化管理就是落實管理責任,將管理責任具體化、明確化,它要求每一個管理者都要到位、盡職。第一次就把工作做到位,工作要日清日結,每天都要對當天的情況進行檢查,發(fā)現(xiàn)問題及時糾正,及時處理等等。 5、“精細管理工程”指企業(yè)按照“六精五細"的思路與方法,對企業(yè)的管理進行精細化改造的工程。 六精:培養(yǎng)企業(yè)精神、運用管理精髓、掌握技術精華、追求質量精品、精通營銷之道、精于財務核(預)算;五細:細分市場和客戶、細分企業(yè)組織職能和崗位、細化分解每一個戰(zhàn)略目標、細化企業(yè)管理制度、細控成本。 …………………… 針對以上觀點,筆者認為更多的是在理念上進行闡述,如果結合企業(yè)管理實踐來認識,缺乏系統(tǒng)的落地的方法和工具,不具有操作性和實用性。 二、卓標顧問對精細化管理的定義和剖析 從企業(yè)實踐的角度來認識精細化管理,卓標首席顧問師李見明及其團隊在研究零缺陷管理和精益生產(chǎn)以及咨詢實踐的過程中,認為:精細化管理(國內(nèi)有人也稱為精益化管理、精準化管理、零缺陷管理、精細化管理工程等),是指以精益求精的態(tài)度,用系統(tǒng)化、規(guī)范化、標準化、專業(yè)化的過程,達成一次做對的結果,即第一次就達成符合客戶的需求,它強調過程和結果的融合。它不僅是一種工具,更是一種理念、一種文化。其目的就是追求以最小的投入,達到最大的產(chǎn)出。其核心就是精細(抓住精要,注重細節(jié))。 該定義強調過程的四化:系統(tǒng)化、規(guī)范化、標準化、專業(yè)化。 系統(tǒng)化強調全局,避免只見樹木,不見森林,陷入細節(jié)的誤區(qū); 規(guī)范化強調制度、流程、職責的建設是基礎; 標準化強調具體、可衡量,避免抽象,難以量化; 專業(yè)化強調人的分工,把合適的人配置到合適的位置上, 避免讓一頭豬去爬樹而不讓猴子去爬樹,注重精細化管理中人的因素。 定義中也強調結果的“一次做對”,即第一次就達成符合客戶的需求。注重執(zhí)行的效率,依靠過程的保障,強調第一次執(zhí)行到位,避免浪費,追求最小的投入,達到最大的產(chǎn)出。 從定義中可以剖析:目前對精細化管理認識的誤區(qū): 誤區(qū)1:精細化管理等于細節(jié)管理。 剖析:精細化管理不能理解為等同于細節(jié)管理。因為精細化管理是在系統(tǒng)化管理指導下的細節(jié)管理,注重全局性。 誤區(qū)2:精細化管理是越精細越好。 剖析:精細化管理不能理解為越精細越好,其目的是追求最小的投入,達到最大的產(chǎn)出,過了(過細)就是浪費,不及(過粗)就是缺陷,強調無過無不及,恰到好處。 誤區(qū)3:精細化管理與規(guī)范化管理無關。 剖析:現(xiàn)代管理學認為,科學化管理有三個層次:第一個層次是規(guī)范化,第二層次是精細化,第三個層次是個性化。而精細化管理是以規(guī)范化管理為基礎,處在科學化管理的第二個層次,是與規(guī)范化管理密切相關的。 三、精細化管理的理論淵源 精細化管理必須借鑒人類工業(yè)史上一切有價值的管理學成果,其中最為緊密的應該是泰勒的科學管理、戴明的為質量而管理,尤其是以精益生產(chǎn)為旗幟的豐田生產(chǎn)方式(簡稱TPS)。在這條線上有一個共同的靈魂,那就是科學與效率。所不同的是,泰勒由于時代的局限只注重到工人的現(xiàn)場操作,戴明擴大到質量的每一根神經(jīng)末梢,豐田生產(chǎn)方式則系統(tǒng)地延伸到了企業(yè)的生產(chǎn)系統(tǒng),而我們現(xiàn)在提出的精細化管理則試圖使以上理論貫穿于企業(yè)管理的全部系統(tǒng)。 1、泰勒的科學管理 弗雷德里克•W•泰勒(Frederick W. Taylor)(1856-1915),美國工程師和發(fā)明家。名言:“幾乎沒有一個熟練的工人不是投入大量時間研究可以如何慢速工作,并且還使雇主相信他的工作速度恰到好處的。”代表作:《科學管理的原則》(The Principles of Scientific Management)。 少年時期他就開始了古典的歐洲之行,行程持續(xù)三年之久。后來他通過了哈佛的入學考試,但由于視力差沒有入學。泰勒先后獲得了一百多項專利。 泰勒提出了提高工作效率的途徑: 分析某一特定工作,找10或者15個特別擅長這一工作的人; • 研究每個人精確的一系列基本操作或運動,以及每個人使用的工具; • 用跑表來計算每個基本活動所需要的時間,然后選擇完成那一工作每一部分的最快方式; • 去掉所有錯誤的、緩慢的、無用的動作; • 把最快最好的動作和最好的工具收集成一個系列。 斯圖爾特說,詰難泰勒現(xiàn)在是一種時尚,但重要的是要記住“科學管理”是一大飛躍,不僅僅是從生產(chǎn)力方面,而且就勞動力的尊嚴而言都是如此。 2、戴明的為質量而管理 W.愛德華茲•戴明(W.Edwards Deming)(1900-1993),美國顧問和學者。代表作《轉危為安》(Out of the Crisis)。 戴明先在懷俄明大學學習電子工程,后獲耶魯大學數(shù)學物理學博士。1939年,戴明成為美國人口普查的首席統(tǒng)計學家。1945年紐約大學統(tǒng)計學教授。1947年應麥克阿瑟將軍的邀請,戴明首次訪問了日本。 戴明的觀點是“為質量而管理”,管理層要對出現(xiàn)的問題負90%的責任。1950年,他對日本的工業(yè)家做了一系列有關“質量控制”的講座。日本科學家與工程師聯(lián)合會則于1951年設立了年度“戴明獎”。在1980年,當美國國家廣播公司就日本作為經(jīng)濟強國的崛起制作一出電視節(jié)目(《如果日本能,我們?yōu)槭裁床荒埽俊罚r,戴明才被重新發(fā)現(xiàn)。 戴明著名的14要點: • 創(chuàng)造產(chǎn)品與服務改善的恒久目標。 • 采用新的(管理)哲學。 • 不要依靠檢驗去保證產(chǎn)品質量。 • 不要只以價格高低來決定采購對象;相反,要與單個供應商合作,以最大限度地降低總成本。 • 持續(xù)不斷地改善計劃、生產(chǎn)和服務的每一個環(huán)節(jié)。 • 實行崗位培訓。 • 運用并構建領導藝術。 • 驅走恐懼心理。 • 消除員工之間的隔閡。 • 不能只對員工喊口號、下指標來提高質量。 • 不要對員工和管理人員設定量化的任務和管理目標。 • 要使員工都能感到他們的技藝和本領受到尊重,取消年度評比或評優(yōu)機制。 • 要有一個強而有效的教育培訓計劃,以使每個員工得到自我提高。 • 使公司的每個員工在自己的工作崗位上各得其的,以完成公司的改革。 豐田汽車設在東京的總部大樓,大廳里顯眼的地方掛著三幅肖像畫:豐田公司的創(chuàng)始人、豐田公司現(xiàn)任總裁和W.愛德華茲•戴明。 我們對質量的理解: 質量是產(chǎn)品和服務滿足顧客需要的程度。 質量保證是為了達到或維護質量,由組織制定的一整套政策、規(guī)則的系統(tǒng)。包括質量工程和質量管理。質量工程指保證質量的一系列的設計;質量管理指對質量的評判及其處理。目的都是通過預防活動和修正措施來達到和維護質量標準。 質量差異來源于可指出因素和一般因素。工具磨損、機器安裝不當、原材料質量不達標、人員操作失誤等屬于可指出因素;材料限制、環(huán)境條件、人員情緒等引起的隨機性和可能的差異,很難控制,為一般因素。統(tǒng)計質量管理關注可指出因素。 3、豐田生產(chǎn)方式 豐田生產(chǎn)方式(TPS—Toyota Production System),即中國認為的精益生產(chǎn),始于豐田佐吉,經(jīng)豐田喜一郎,到大野耐一成形。 《豐田生產(chǎn)方式》出書始于1978年3月,中國翻譯出版始于2006年8月。在大野耐一主持下40年代中開始的“多品種,少批量”的豐田生產(chǎn)方式,目的在于“徹底杜絕企業(yè)內(nèi)部各種浪費,以提高生產(chǎn)效率”。 “準時化(JIT)和自動化(Jidoka)”是貫串豐田生產(chǎn)方式的兩大支柱。準時化:就是在通過流水作業(yè)裝配一輛汽車的過程中,所需要的零部件在需要的時刻,以需要的數(shù)量,不多不少地送到生產(chǎn)線旁邊。自動化:不是單純的機械“自動化”,而是包括人的因素的“自動化”。 “人性自動化”的精神產(chǎn)生于豐田公司的創(chuàng)始人豐田佐吉(1867-1930)發(fā)明的自動織布機(經(jīng)線斷了一根或者緯線用完,織布機立即停止運轉)。機器的高速化使得工廠稍微發(fā)生一些異常情況就非常麻煩:不同規(guī)格的材料混進了機器、邊角料卡住模具,設備和模具就會損壞;絲錐一旦折斷,就會造出沒有螺紋的不合格品眨眼間堆積如山。豐田公司的任何一個工廠幾乎所有的機器設備(包括新的和舊的)都裝有自動停止裝置:“定位停止方式”、“全面運轉系統(tǒng)”、“質量保險裝置”。人只是在機器發(fā)生異常情況、停止運轉的時候才需要,一個人可以管理好幾臺機器。自動化的關鍵在于賦予機器以人的智慧,同時還要設法讓操作者的單純“動作”變成“工作”,使人與設備有機聯(lián)系起來。為了便于理解,我們把豐田汽車的兩大支柱通俗解釋為:準時化就是剛好來得及;自動化就是故障自己停。 “均衡化生產(chǎn)”是豐田生產(chǎn)方式的一個重要條件。“看板”方式對于縮減工時、減少庫存、消滅次品、防止再次發(fā)生故障起到巨大作用。徹底找出無效勞動和浪費現(xiàn)象并著手消除是豐田的務實態(tài)度。 把物、機器和人的作用組合起來的過程稱之為“作業(yè)的組合”,而這種組合集中起來的結晶就是“標準作業(yè)”。標準作業(yè)表的三個要素: 周期時間:指生產(chǎn)一件工件或一輛汽車需要的時間,這是由生產(chǎn)量(即需求量)和機器的開動時間來決定的。一天的需求數(shù)量,以勞動時間除一個月的需要數(shù)量就能算出來。所以,周期時間是一天的需要數(shù)量除勞動時間得出的結果。 作業(yè)順序:指操作人員在運送工件、機器上下物件時,按時間先后排列的工件加工順序(但這不是產(chǎn)品沿著流水線移動的作業(yè)順序)。 標準存活量:指作業(yè)時一些必要工程上的在制品以及停留在機臺的物品數(shù)量。 4、精細化管理誕生 從制造業(yè)生產(chǎn)系統(tǒng)精益生產(chǎn)方式向企業(yè)的整個運營系統(tǒng)擴展,邁出了從精益生產(chǎn)到精益思想的過渡,進而延伸到服務業(yè)等各個領域,標志著精細化管理的誕生。 |
上一篇 : 創(chuàng)業(yè)公司招聘的注意事項1-老板親自面試
下一篇 : 現(xiàn)場管理如何開展工作